SOLUTIONS 課題解決事例
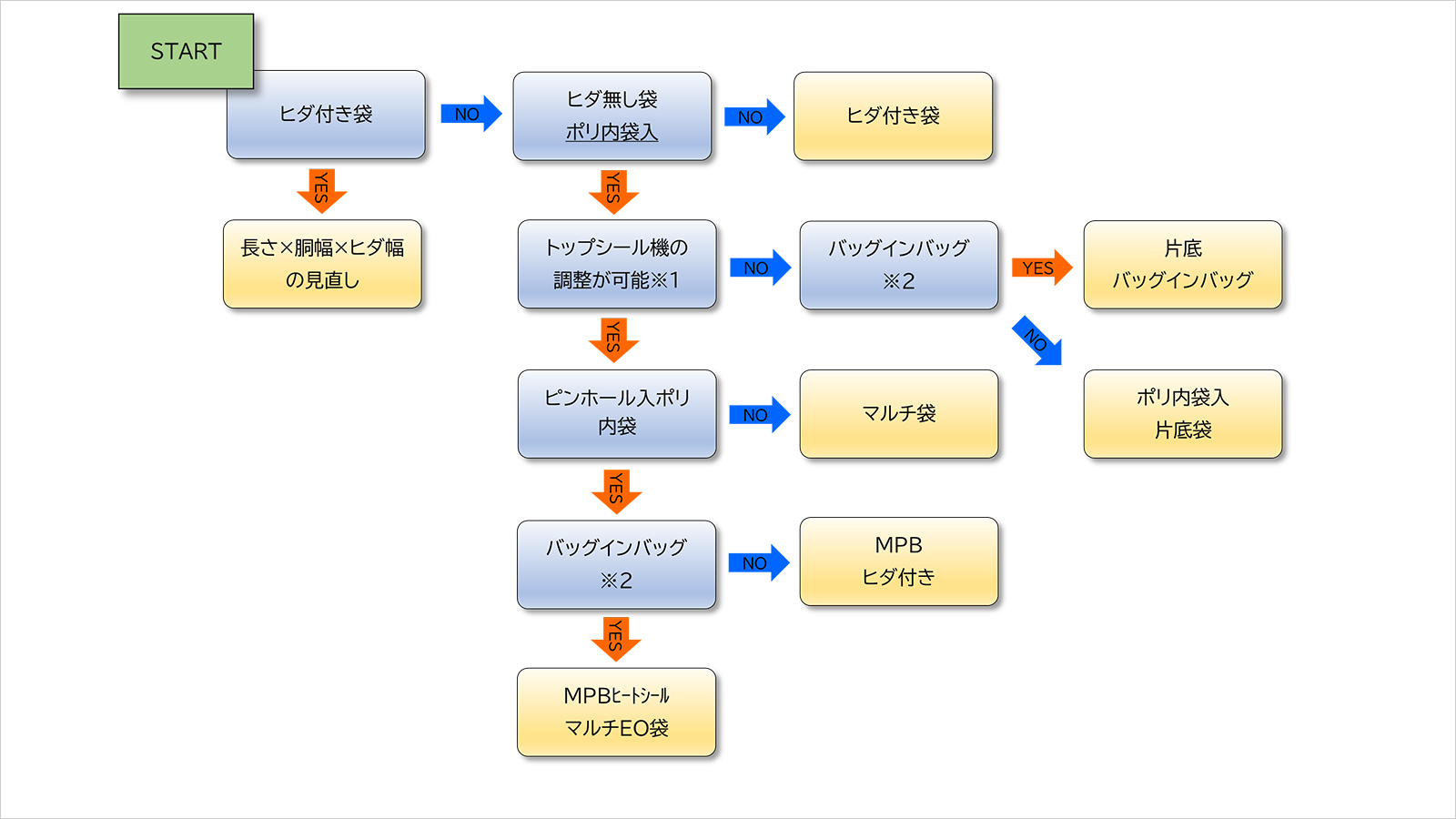
昨今の物流はホワイト物流化が進み、人手によるトラックへの積み降ろしはほとんどなく、パレット輸送が主流となっています。パレット規格も11型(1100㎜×1100㎜)や14型(1100㎜×1400㎜)がトラックへの積載効率が良く、広く利用されています。
しかし、現行の荷姿(紙袋20kg~25kg入の個包装)では効率良くパレットに積載できないため、パレット輸送に移行できないと相談をいただくことがあります。
そこで「荷姿改善によるパレット積載の最適化」の課題解決事例をご紹介します。効率良くパレットに積載できればパレット輸送が実現し、ホワイト物流化のゴールが見えてくると思います。
パレット積載の問題点
- ・現行規格では3俵配・4俵配・5俵配でもかなりの空きスペースができてしまい、積載効率が悪い
- ・積載してもパレットからはみ出してしまい、コンテナへの積み込みができず、また荷傷みが危惧される
- ・形式変更で「ヒダ無し袋→ヒダ付き袋」を検討したいが充填後のヒートシール状態に不安がある
改善のポイント
改善のポイントは荷姿の“高さ”の調整です。“高さ”調整でパレット積載の最適化を進めます。
荷姿の“高さ”はヒダ付き袋の場合は「ヒダ幅」が影響し、また「ヒダ無し袋」の場合は“高さ”が出しにくいため「ヒダ付き袋」に変更、または片底袋に変更する事で“高さ”を形成していきます。
YES/NOチャートで現行紙袋から最適な紙袋の提案をご案内します。
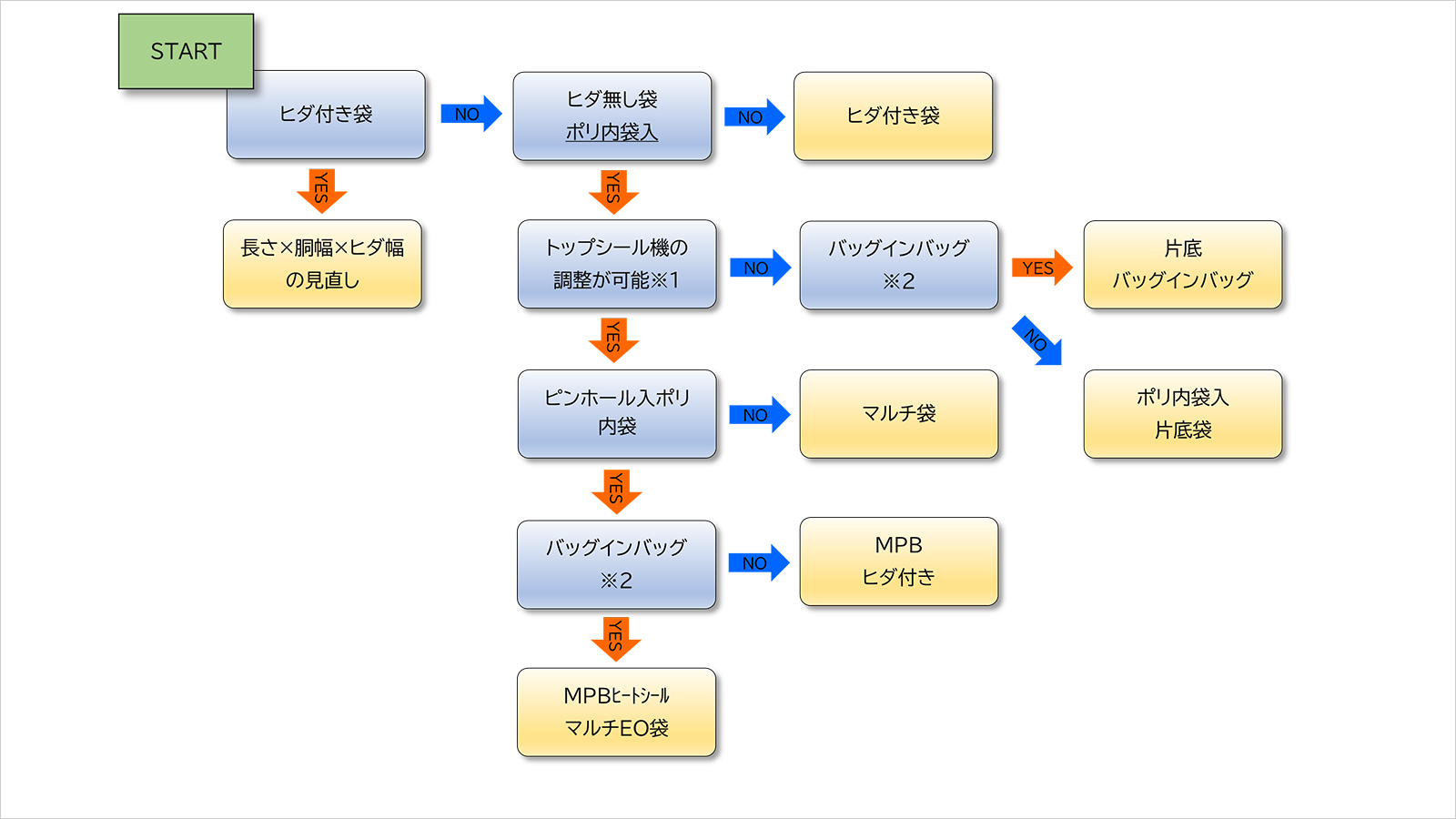
※1 充填後のヒートシールにおいて「ヒダ無し袋からヒダ付き袋」に変更した場合、ヒダ部の接着が不安定になる事があります
※2 充填後にポリ内袋のみ取り出せる仕様となります
効果
現行紙袋の機能を損なうことなく、パレット規格に荷姿を合わせていくことが改善の近道です。
紙袋の機能は脱気・防湿・開封性・コンタミ防止など様々ですが、すべての機能を維持しながら、新しい紙を提案できるのがシコーです。
最後にバッグインバッグミシン袋から片底バッグインバッグに変更した事例をご紹介します。
従来ではパレットから製品がはみ出してしまい、パレットでのトラック積載ができませんでしたが、改善後はパレット規格内に製品を積み付けできるようになり、パレットでトラックに積載ができようになりました。
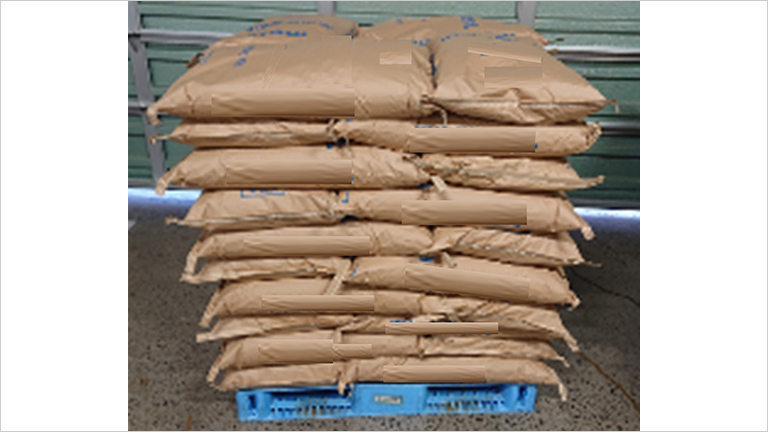
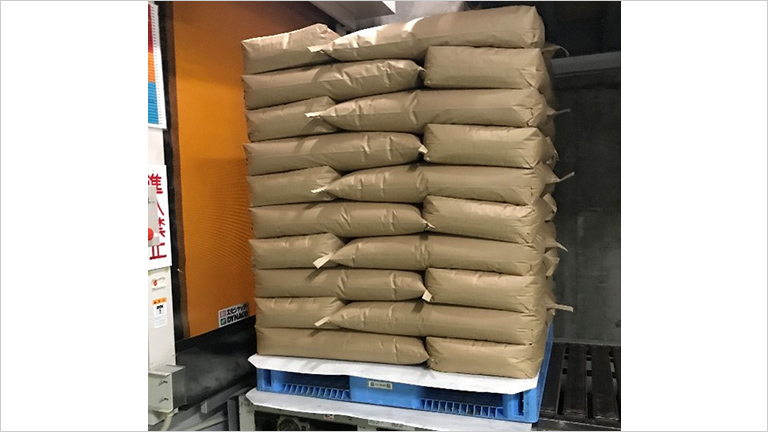